
| |
GN Electric Operations continued
The carbon pile relay is really the voltage regulator.
Spring action forces the carbon discs together. These discs
are in the exciter field circuit and the greater their
pressure together, the lower their resistance, hence, higher the
exciter voltage, so the spring compressing carbon discs
together causes maximum voltage on exciter. The regulating
coil is connected across the exciter armature, and its
mechanism is hooked up to overcome the spring pressure
which tends to reduce the compression on carbon discs
and increase their resistance. The higher the exciter voltage,
the greater this counter pull of coil is to spring, so
that the result of the spring trying to compress carbon
discs, and the coil trying to overcome the spring, is a
constant regulated voltage at any desired value. Failures
occur in two ways: (1) A broken coil circuit lets the spring
have full sway, the exciter voltage will run way high, and
battery will be wrecked by boiling it, if not quickly
corrected. You will smell battery acid heating up if this
occurs. If the spring should break, the exciter will not
build up, relay PR3 cannot close and M-G set will
probably run up to overspeed on starting motor kicking out
M-G overspeed, same as if carbon pile fuse blown.
Shopmen; never work on any relay without a voltmeter,
to set it properly.
Road men proceed as follows: If RCR fails to pick up
account open circuit coil, let M-G set reach full speed,
then block RCR in by hand with wedge. Be sure carbon
pile fuse is okay.
Carbon pile relay trouble: M-G running full speed, broken
circuit in regulating coil will cause battery charge rate to
be excessive, 200 to 250 amperes. Take wedge and place so
that coil plunger will be forced up into coil just enough
so that charge rate is 50 amperes. If spring breaks, put
wedge so that plunger will be pulled down out of regulating
coil just enough to pick up RCR and 50 ampere charge
on battery. Wooden wedges placed on either side of pivot
armor relay to raise or lower plunger. Be careful, as small
movements cause big voltage changes.
Relays X1, X2 along with X-fuse, are actually
compressor speed control relays which are only cut in when
compressor selector switch is thrown to the emergency
regeneration position and in no way affect normal
compressor A. C. operation. Both of these relays merely
control the field resistance of the No. 2 traction motor, which
Page 65
acts as a generator. Relays X1, X2 are operated by traction
motor voltage, and they in turn control resistance switches
Nos. 49, 50, which keep the traction compressor voltage
constant, and compressor speed constant, regardless of
locomotive speed, when this emergency feature is used. If
the X-fuse blows, the X1, X2 relays are inoperative and
compressors will run at increasing speed as locomotive
speed increases. Hence, these relays and their fuse are
merely speed governors for compressors under emergency
operation.
Westinghouse Trouble Shooting
SAFETY FIRST AND ALWAYS. Your first and last
chance are same one with high voltage, and no voltage,
low or high, is safe to touch, as there might be more there
than you think.
M-G set fails to start: The Westinghouse M-G set is
normally started, by using the main generator as a motor,
and driving it from the battery. In order to make this
connection, the main field contactors G1 and G2 must
close, as well as all the other G contactors but G3. Also
starting switches ST1 and ST2 must close. The starting
controller closes all of these contactors and switches on
its first notch, applying full field to the generator, and
reduced voltage to generator armature. Notches 2, 3, 4
included, successively cut resistance out of armature circuit
until full voltage of battery is now applied to armature,
as well as full field. From notch 5 to 9, the generator
field is weakened by means of opening G contactors. This
speeds up M-G set to 250 R. P. M. when relay SR1
changes connections to cut out battery and generator, and
connects synchronous motor to transformer reduced
voltage tap.
(A) Failure of M-G set to start, means that one or more
of the necessary switches and contactors have not closed.
Be sure relays ACOL, line relay, and M-G overspeed, are
closed and on good contact. Pulling M-G stop switch open
and closing it, if ML switch is heard to open and close,
proves relays are okay.
Starting controller is energized as follows:
Wire AP from M-G stop switch to contacts AP, AP1
on controller reverse drum off position, AP1 from reverse
drum to L out interlock, AP12 from L out to SL out inter-
lock, and feed wire AP2 from SL out to M-G start
controller. AP2 energizes the controller. All other wires on
Page 66
it take current to the different switches and contactors.
Hence, if any G contactors, or ST switches are closed when
start controller is on first, or any notch, it indicates start
controller is energized. However, G1, G2, ST1, ST2 must
all be closed to start machine. If controller is energized
and G1, G2 fails to close on first notch, trouble is usually
the 2C and N contacts on start controller interlock drum,
or finger No. 11 on start controller has a bad contact. If
either of G1 or G2 contactors should be found open alone,
while the other one is closed, it is an open circuit magnet
coil on the open switch, or the other switch is welded in.
Should ST1, ST2 switches fail to close on first notch,
while G1, G2 are closed, trouble is likely on Gl in
interlock or controller is either not on first notch fully, or the
first notch has been over-run too fast for switches to pick
up (their air cylinders take time to fill). ST1 and ST2
close on first notch, but drop out when controller is moved
to next higher notch. This is a case of bad order ST1 in
interlock. ST3, ST4 cut out resistance in armature of
generator on second, third, fourth notches. If M-G does
not start on fourth notch, shut off and try another cab.
When the other cab M-G gets running it will give better
voltage to help start troublesome cab. Be sure all proper
switches are closed on switch board before trying to start
M-G set.
(B) M-G starts okay, but fails to connect to transformer:
SR1 will not close. When M-G set reaches full battery
speed 250 R. P. M. relay SRI should close and connect
synchronous motor to transformer, set will speed up. If
SR1 does not close, get set up to full battery speed, leave
start controller wide open, close SR1 bv hand at 250
R. P. M. and hold SR1 in, until after SR2 closes and set
steadies down at full speed. Then let SR1 drop out. SR1
relay may close, and connect synchronous motor to
transformer, speeding up M-G set to 600 R. P. M., then just
as SR2 relay closes, SR1 drops out, opening switch SL with
a loud report and M-G set stops as if overloads tripped.
Remedy: Watch relay SR1, and make a normal start of
M-G set, then as relay SR1 closes, hold it closed until
ten or fifteen seconds after SR2 closes and M-G set reaches
full speed. This trouble is caused by a broken SR1 resister
tube.
(C) M-G set starts, connects to transformer okay, but
will not properly synchronize with line: This type of
trouble is due to one of two relays either failing to close,
or closing on bad contacts. They are relays SR2 and AR.
Page 67
Relay SR2 normally closes at 600 R. P. M. and it closes
synchronous motor field switch SM1. If SM1 is closed,
the synchronous field amperes will indicate 50 amperes.
Normally this 50 ampere indication will only last until
relay AR closes its contacts to change synchronous motor
connection over from switches ML, SL reduced voltage
tap, to full running voltage tap switches ML, RL, L,
SM1, SM3 all closed and synchronous field amperes will
indicate 100 to 150 amperes D. C. If relay SR2 fails
to close, then wait until M-G set is up to about full speed
and close relay SR2 by hand. Be careful not to let relay
contacts open after you close it, or switches may be
damaged by chattering in and out, then block relay closed.
Failure of SR1, or SR2 usually caused by relay resister
tube breaking.
Relay AR can fail in three ways: (1) its air supply fail,
(2) the magnet valves, any one of the three of them, burn
out and become inoperative, (3) it may close on a bad
contact, or if SM1 in interlock is dirty, it will not close
AR at all. If AR relay air pipes break after relay SR2
closes switch SM1, put a tooth pick or match stick in SM1
in interlock to stop air blowing from AR pipes, then
carefully short or jumper the fingers on AR together, and be
sure to only connect the ones to each other, that normally
would be connected if relay worked okay. If it is liable
to be contact trouble, clean SM1 in interlock to operate
AR. Clean both AR interlocks to operate switches RL,
L, SM3.
(D) Engine will not move. M-G set runs okay With
M-G set running normally, switches ML, RL, L, SM1,
SM3, El, E2 all closed, all traction motor cut out switches
closed, two things must be accomplished: (1) The main
generator and the traction motors must be connected
together by line switch L1 closed. (2) The main generator
must be supplied field current by G1, G2 both closed, as
well as numerous other G contactors. Mainly, L1, G1, G2
must close to move engine. The master controller operates
all G contactors and line switch L1. Battery control
current is red to master controller from control reset switch
and fuse to contact B1. P2 on reverse control drum, in
either forward or reverse position. From here P2 wire
makes contact with P3 wire on start control interlock drum
in off position, and P3 wire runs from interlock drum to
energize speed drum of master controller. All other wires
on speed drum carry current away to operate their
respective switches and contactors, fed by P3.
Page 68

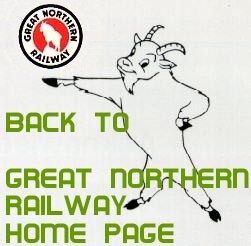 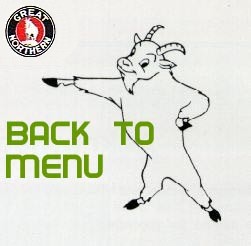
|