
| |
GN Electric Operations continued
Special: Since L1, G1, G2, L2, RG1, RG2 all have a
common negative return wire through the following
contacts, four traction overloads, L1 in interlock, E1, E2 in
interlocks, N1, N contact on master controller, if any one
of the stated contacts in negative return circuit are tripped
or bad order from any cause, none of the switches L1, L2,
RG1, RG2, G1, G2 can be closed. Likewise, if any of
these switches are closed, as say G1, G2, but L1 failed to
close, the trouble is not in their return circuit but in the
supply, as L1 not closed account of RG1 out interlock
dirty or broken, or transition relay top contact dirty or
broken. Also L1 may be closed but G1, G2 open account
of dirty or broken interlock on ML in or A3 out. Take one
notch on controller with engine brake set, and look to see
if all necessary switches are closed, remembering that
M-G set must be running normal first with switches ML,
RL, L, SM1, SM3, E1, E2 closed. Then to move engine
G1, G2, L1 must close and before any of the traction
switches or generator field contactors can be closed, the
control reset switch and its fuse must both be closed
making good contact, along with the reverse lever thrown to
proper position, and the speed controller notched out.
(E) Engine runs okay in straight motoring, but it will
not operate in separate field control, or regeneration: For
operating in straight motoring where only the speed lever
is used, and the ratio of armature amperes to field amperes
is 1 to 1, switches L1, G1, G2 had to be closed and making
good contact, as well as other necessary G. Contactors as
control print, if checked, will indicate.
Separate field control is used where tonnage, grades and
peak load permit higher speed. It is the equivalent of
hooking up a steam engine to control its cut off. Likewise,
in separate field control, you control the field amperes
within the permissible load and field to armature ampere
ratio, to increase speed. The switches involved in this
change of connections are L2, RG1, RG2, other necessary
RG contactors as control print indicates, and stabilizing
switches (which are practically field by-pass switches) L31,
L32, L33, L34. The controls governing change over are
the field controller, transition relay and the separate control
button for establishing connection, as well as the series
button to change back to straight motoring from separate
control motoring.
In order to operate locomotive in either separate
motoring or regeneration, the following conditions must prevail
in their orderly sequence. Notching out on field lever of
Page 69
master controller energizes the transition relay, closing
lower contacts of relay, which in turn closes D. C. line
switch L2, and the L2 in interlock opens D. C. line switch
L1. This change connects the regenerative exciter into
the field circuit of the traction motors whose field strength
it will regulate in separate motoring or regeneration. With
switches L1 out, L2 in, G1, G2 in, contactors RG1, RG2
close through wire 4 from field controller and the L2 in,
L1 out, ML in and G2 in interlocks. Further notching of
field lever builds up the regenerative exciter voltage, which
when equalized with field voltage drop as indicated by
balancing voltmeter indicating zero where it formerly
indicated on low side, then the separate control button is
pushed in to close stabilizing switches L31, L32, L33, L34.
The control circuit for stabilizing switches is: wire No. 4
from field drum energizes separate control button, and wire
4C from separate button through interlock L2 in to wire
4D which runs branch circuits to each individual stabilizing
switch, through the control interlocks on the individual
traction motor cut out blade switches, as: motor cut out
No. 1 closed to L31 and following cut out No. 2 to L32, cut
out No. 3 to L33, cut out No. 4 to L34. From the stabilizing
switch coils, the control current completes its return
circuit through wire 4K to series button, and wire 4L from
series button to N wire on reverse control drum. From
the circuits described, failure of any particular switch can
be traced.
(F) Examples. L2 fails to close: If G1, G2 are closed
the common negative return from wire 2C to wire N1 for
L1, L2, RG1, RG2, G1, G2, through the four D. C. traction
motor overload contacts, L in E1 and E2 in interlocks are
all okay, or G1, G2 would not be closed. Hence, L2
trouble is mostly likely transition relay contacts.
(G) L2 closed okay; but RG1, RG2 fail to close. This
trouble will be found in one of the following places or
interlocks; L2 in, L1 out, ML in or G2 in interlocks. If
either one of these contactors are closed and the other
one is open, the open contactor will probably be found with
a bad order coil. Since both RG1 and RG2 contactors have
important control interlocks on them, no recommendation
is made for blocking them in. Just run straight motoring.
(H) L2 and RG1, RG2 close okay, but stabilizing switches
fail to close. Stabilizing switches can fail to close
individually if the traction cut out interlocks are not making
contact account switch not fully closed or dirty contact, or
Page 70
stabilizing switches all four fail to close due to
interruptions
in their supply circuit at separate button, L2 in interlock,
or a similar interruption in their negative return circuit
at series button, or on reverse control drum 4L and N
contact. Usually dirty L2 in interlock is most likely place
for trouble in this circuit.
Trouble Shooting General Electric and Westinghouse
Control jumpers: Failure of control jumpers. occurs in
two ways.
Symptoms: (1) Open circuits or corroded contacts cause
the switches normally operated by these wires to become
inoperative in the cabs trailing the control cab.
(2) Short circuits within control jumpers cause false
sequence in all cabs connected by jumpers often damaging
the locomotive, as: example, a switch that normally closes
on full throttle, if this switch operating wire gets
accidentally in contact with a wire operating another switch
on say first notch, then on first notch engine will get full
power.
Special instructions: Whenever jumper troubles show up,
(a) remove all jumpers completely from all cabs'
receptacles. Do not just pull one end. (b) Test each
individual cab from its own controller to make sure all
cabs okay. (c) Then put in all jumpers between cab No.
1, cab No. 2 and make test of switch sequence. Switch
sequence should be for motoring switches and generator
field contactor, (d) Regeneration switches, and regenerative
exciter field contactors. If this works okay between
cabs 1 and 2, put in jumpers between cabs 2 and 3, then
make switch sequence test. Should this give faulty operation,
your trouble is in this set of jumpers. Pull them out
completely, as they will cause trouble.
If you can get along on the two cabs, shut down the
one with no jumpers, or as has happened before in a pinch,
engineer ran the jumpered cabs, if head cab was one of
them, and fireman operated the others independent. The
idea is KNOW SEQUENCE, so you can tell when you
see the trouble what it is, and SAFETY FIRST AND
LAST. Be careful and do not take any chances ever.
Westinghouse Relays
Westinghouse cabs are equipped with the following
relays, whose functions, operation and troubles will be
covered:
Page 71
Oil circuit breaker trip, called "trolley trip" located in
relay cabinet: This is an A. C. current transformer operated
relay on main transformer primary, which trips when
excessive current flows from trolley to transformer. It
protects the transformer from trouble within itself, and will
also trip if the synchronous motor, D. C. generator, or
traction motors develop serious defects, that their own
particular overload relays fail to clear. The operation is
as follows: Normally with the circuit breaker relay
contacts closed, battery control current flows through these
contacts to the circuit breaker holding coil. If an overload
trips the circuit breaker relay, the circuit breaker hold coil
is de-energized, and this causes the control latch of circuit
breaker mechanism to open, thereby opening oil circuit
breaker main contacts. When circuit breaker relay is reset
by its handle being raised full up, the circuit breaker may
then be closed. If this relay is tripped, the circuit breaker
will not stay closed.
However, there is one other trouble which has same
symptoms as an open or oxidized circuit breaker trip, and
that is a defective control latch in circuit breaker
mechanism. This latch under such conditions may safely be tied
in with a single string or loop of cloth (never wire).
ALSO NEVER WORK AROUND HOT CIRCUITS. HAVE
PANTOGRAPHS DOWN AND GROUND SWITCHES
CLOSED.
Synchronous motor overload trip, called ACOL, located
in relay cabinet is an A. C. current transformer operated
relay. The current flowing into synchronous motor
operates this relay. It trips and shuts down M-G set, if not
quickly reset by overload reset switch. Its function is to
protect synchronous motor from overloads. Too fast
notching of controller will trip it, as will flashovers or short
circuits on D. C. generator or motors. The only trouble
it gives is dirty disc and finger contacts, or a broken disc.
Spinning the disc usually cleans the contact.
Exciter overload, called DCOL, located in relay cabinet,
protects main exciter from overloads due to a short
circuit in any of the field circuits of generator, synchronous
motor, or regenerative exciter; also the battery circuit or
compressor. It is a D. C. current relay operated by the
exciter output current. The only trouble experienced is
dirty contact discs or fingers. It this relay is tripped, an
"E" switch will be open, that cab cannot pull and
battery ampere gauge will show discharge.
Page 72

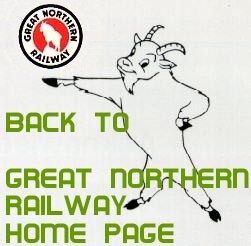 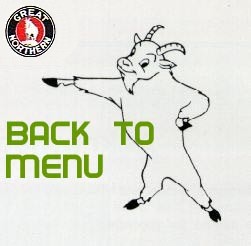
|